Design Control: Entwicklung strukturiert steuern
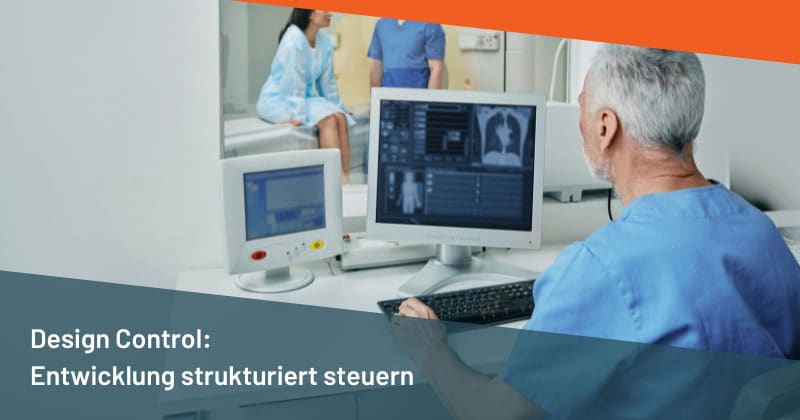
Design Control ist in der Medizintechnik ein verbindlicher Rahmen für die Steuerung von Entwicklungsprozessen. Ziel ist es, technische Anforderungen, regulatorische Vorgaben und Herstellbarkeit von Anfang an zusammenzudenken – und in nachvollziehbaren Schritten zu dokumentieren.
Ein strukturierter Design-Control-Prozess schafft die Grundlage für sichere Produkte, reproduzierbare Verfahren und belastbare Zulassungsunterlagen. Gleichzeitig ermöglicht er, Risiken frühzeitig zu erkennen, Anforderungen systematisch zu prüfen und spätere Änderungen effizient zu beherrschen
Die Anforderungen sind hoch: Jede Funktion, jedes Material, jede Schnittstelle muss geplant, überprüft und nachvollziehbar freigegeben werden. Ohne ein wirksames Design Control-System entsteht schnell ein Risiko – für Patientensicherheit, Zulassungsverfahren und Auditfähigkeit.
Dieser Artikel zeigt, wie sich Design Control in der Praxis umsetzen lässt – eingebettet in ein leistungsfähiges Qualitätsmanagement Medizintechnik, unterstützt durch Prozessvalidierung, Root Cause Analysis, Audits Qualitätsmanagement und Prozessanalyse.
- Design Control in der Medizintechnik: Warum sie unverzichtbar ist
- Die zentralen Elemente der Design Control: Von der Idee zur Freigabe
- Typische Schwächen in der Design Control – und wie man sie vermeidet
- Design Control strategisch nutzen – als Brücke zwischen Entwicklung, Qualität und Zulassung
- Fazit: Design Control als Rückgrat strukturierter Produktentwicklung
Design Control in der Medizintechnik: Warum sie unverzichtbar ist
Die Entwicklung von Medizinprodukten ist hochreguliert – und das aus gutem Grund. Schon kleinste Konstruktionsfehler oder unklare Anforderungen können weitreichende Folgen haben: von technischen Rückfragen in der Zulassung bis hin zu Risiken für Patienten. Genau hier setzt Design Control an.
Design Control bezeichnet den strukturierten Rahmen, in dem Entwicklung, Verifikation und Validierung eines Produkts ablaufen – mit klar definierten Meilensteinen, Rückverfolgbarkeit und nachvollziehbarer Dokumentation. Die Vorgaben, etwa in 21 CFR 820.30 oder ISO 13485, verlangen unter anderem:
- definierte Benutzeranforderungen
- technische Produktspezifikationen
- Planungs- und Änderungsprozesse
- Dokumentation von Verifikations- und Validierungsaktivitäten
- Freigaben und Übergabepunkte für jede Phase
Der entscheidende Punkt: Design Control ist kein reines Dokumentationswerkzeug. Es soll verhindern, dass Sicherheits- oder Leistungsanforderungen übersehen werden – und zugleich sicherstellen, dass Produkte später überhaupt wirtschaftlich, reproduzierbar und regelkonform hergestellt werden können.
In der Praxis wirkt Design Control wie ein Filter: Es zwingt zur Klarheit über das, was entwickelt wird – und wie es überprüfbar bleibt. Besonders dann, wenn Produkte komplexer, interdisziplinärer oder softwarebasiert sind, steigt die Relevanz.
Unternehmen, die Design Control frühzeitig, konsistent und vollständig anwenden, minimieren technische Risiken, beschleunigen die Zulassung und verbessern die Auditfähigkeit. Fehlstellen in diesem Prozess führen dagegen häufig zu späteren Korrekturen – etwa durch aufwendige Prozessvalidierungen, zusätzliche Tests oder CAPAs.
Die zentralen Elemente der Design Control: Von der Idee zur Freigabe
Ein funktionierender Design Control-Prozess strukturiert den Produktentstehungsprozess in klar definierte Phasen. Ziel ist es, zu jedem Zeitpunkt zu wissen, wo sich ein Produkt befindet, welche Anforderungen gelten und welche Nachweise erbracht wurden – technisch, regulatorisch und formal.
Die wichtigsten Elemente im Überblick:
1. Design and Development Planning
Bereits zu Beginn wird der Ablauf der Entwicklung festgelegt – inklusive Verantwortlichkeiten, Meilensteinen und Rückverfolgbarkeit. Das Projektteam plant nicht nur Aktivitäten, sondern auch Prüfungen, Reviews und Dokumentationsanforderungen.
2. Design Inputs
In dieser Phase werden Anforderungen erhoben und definiert – aus Benutzerperspektive, regulatorischer Sicht, technischer Machbarkeit und Markterwartung. Die Qualität der Design Inputs entscheidet darüber, wie stabil und effizient das gesamte Projekt läuft.
3. Design Outputs
Das greifbare Ergebnis der Entwicklung: technische Zeichnungen, Stücklisten, Prüfpläne, Fertigungsspezifikationen. Sie müssen konsistent zu den Inputs passen und alle Anforderungen erfüllen, um für den nächsten Schritt freigegeben werden zu können.
4. Design Review
Kritische Zwischenetappen in der Entwicklung werden systematisch geprüft – interdisziplinär, dokumentiert, mit klarer Entscheidung über nächste Schritte. Ziel ist es, frühzeitig Fehler zu erkennen, bevor sie in Produktion oder Validierung eskalieren.
5. Design Verification und Validation
Hier wird geprüft, ob das Produkt das tut, was es laut Spezifikation soll (Verification) – und ob es unter realen Bedingungen die Benutzeranforderungen erfüllt (Validation). Beide Schritte sind verpflichtend, dokumentationsintensiv und regulatorisch hochrelevant.
Eine saubere Trennung zwischen Verifikation und Validierung ist essenziell – insbesondere, wenn Produkte mit Patienteninteraktion, Softwarekomponenten oder mehreren Risikoklassen vorliegen.
6. Design Transfer
Bevor das Produkt in die Serienfertigung übergeben wird, müssen alle Unterlagen, Prüfprozesse, Spezifikationen und Freigaben in einen fertigungstauglichen Zustand überführt werden. Eine enge Abstimmung mit Prozessvalidierung, Einkauf und Produktion ist hier entscheidend.
7. Design Changes
Auch nach dem Transfer bleibt das Design nicht statisch. Änderungen müssen strukturiert geplant, bewertet, freigegeben und rückverfolgbar dokumentiert werden – mit klarer Bewertung ihrer Auswirkungen auf Risiko, Zulassung und Validierungsstatus.
Ein belastbarer Design Control-Prozess ist kein starres Gerüst, sondern ein dynamisches Führungsinstrument. Richtig umgesetzt, schafft er nicht nur regulatorische Sicherheit, sondern verbessert Zusammenarbeit, Fehlervermeidung und Entwicklungsqualität – systematisch und langfristig.
Typische Schwächen in der Design Control – und wie man sie vermeidet
Design Control ist kein Selbstläufer. Auch wenn die Anforderungen in Normen und regulatorischen Leitlinien klar beschrieben sind, zeigen sich in der Umsetzung häufig Lücken – inhaltlich, methodisch und organisatorisch. Diese Schwächen sind nicht nur ein Problem für die Zulassung, sondern auch für die Prozesssicherheit, Auditfähigkeit und spätere Produktverantwortung.
Ein häufiges Problem ist die unklare Trennung zwischen Design Inputs und Outputs. Anforderungen werden oft unstrukturiert gesammelt, nicht versioniert oder nur in Einzelabteilungen gepflegt. Die Folge: Inkompatibilitäten, fehlende Rückverfolgbarkeit und mühsame Nacharbeit bei Audits oder Validierungen. Ein sauber strukturierter Anforderungsmanagementprozess mit klarer Verantwortlichkeit schafft hier Abhilfe.
Auch Design Reviews werden in der Praxis häufig als reine Formalie behandelt – statt als echter Kontrollpunkt. Wenn Reviews ohne interdisziplinäre Beteiligung, ohne klare Fragestellungen oder ohne dokumentierte Ergebnisse durchgeführt werden, verlieren sie ihre Funktion. Sinnvolle Design Control erfordert verbindliche Review-Strukturen – mit Rollen, Bewertungsrahmen und Entscheidungsprotokollen.
Ein weiteres Risiko
…liegt im Übergang von der Entwicklung zur Produktion: Der Design Transfer erfolgt oft zu spät, zu unstrukturiert oder ohne enge Abstimmung mit der Prozessvalidierung. Die Konsequenz sind unnötige Anpassungsschleifen, Fehler in der Umsetzung und Validierungen, die nicht vollständig zur Designdokumentation passen.
Fehlende Änderungsprozesse sind ein weiteres typisches Schwachfeld. Design Changes werden zu spät erkannt, unvollständig dokumentiert oder nicht auf ihre regulatorische Relevanz geprüft. Hier braucht es eine Anbindung an das CAPA Management, klare Kriterien für Re-Validierung und einen dokumentierten Workflow zur Bewertung technischer Änderungen.
Nicht zuletzt ist die Integration mit anderen QM-Prozessen entscheidend. Eine Root Cause Analysis, die nicht auf Designentscheidungen zurückgreifen kann, bleibt oberflächlich. Und ein Auditprozess, der Designphasen nicht abbildet, bleibt unvollständig. Unternehmen, die Design Control als verbindendes Element im Qualitätsmanagement begreifen, schaffen Transparenz – intern wie extern.
Design Control strategisch nutzen – als Brücke zwischen Entwicklung, Qualität und Zulassung
Design Control ist die Schnittstelle zwischen technischer Kreativität, formaler Verantwortung und struktureller Sicherheit. Wer diesen Prozess richtig aufsetzt, schafft eine Verbindung, die weit über die reine Dokumentation hinausgeht.
In der Entwicklung sorgt Design Control für Klarheit: Welche Anforderungen gelten? Was wird überprüft – und mit welchem Ziel? Welche Annahmen liegen dem Produktkonzept zugrunde? Die systematische Bearbeitung dieser Fragen macht Entwicklungen nachvollziehbar, skalierbar und prüfbar – sowohl technisch als auch regulatorisch.
Gleichzeitig ist Design Control ein wesentliches Steuerungselement im Qualitätsmanagement. Es verankert Rückverfolgbarkeit, strukturiert Übergaben und bildet die Grundlage für Prozessvalidierung, CAPA Management, Root Cause Analysis und Audits. Ohne ein belastbares Design Control-System wird jede Form von Abweichungsanalyse, Revalidierung oder Änderungsmanagement zur Einzelfallentscheidung – mit entsprechendem Risiko.
Auch in der regulatorischen Kommunikation wirkt Design Control als zentrale Ressource: Behörden und Auditoren erwarten nachvollziehbare Entscheidungen, dokumentierte Änderungen, Versionsstände und klare Verantwortlichkeiten – nicht als Zusatz, sondern als Voraussetzung für Zulassung und Marktverbleib.
In der Praxis zeigt sich: Unternehmen, die Design Control nicht als administrative Pflicht, sondern als strukturgebendes Führungsinstrument begreifen, gewinnen an Geschwindigkeit, Qualität und Steuerbarkeit. Die Integration mit angrenzenden Systemen – von der Entwicklung über das Qualitätsmanagement Medizintechnik bis zum Technischen Dossier – macht aus einem Regelwerk ein strategisches Element im Produktlebenszyklus.
Fazit: Design Control als Rückgrat strukturierter Produktentwicklung
Design Control schafft Verbindlichkeit in einem Bereich, der oft zwischen Innovation, Geschwindigkeit und regulatorischem Anspruch vermitteln muss. Ein klar strukturierter Entwicklungsprozess verhindert Unschärfen, fördert die Zusammenarbeit zwischen Fachbereichen und liefert belastbare Grundlagen für Zulassung, Produktion und Qualitätssicherung.
Wirklich wirksam wird Design Control dann, wenn es konsequent mit den übrigen Bausteinen des Qualitätsmanagementsystems verzahnt ist: mit Prozessvalidierung, Risikobewertung, CAPA Management, technischer Dokumentation und regelmäßigen Internen Audits, die sicherstellen, dass der Prozess auch im Alltag gelebt wird.
Unternehmen, die Design Control nicht als Pflichtaufgabe, sondern als zentrales Steuerungsinstrument verstehen, schaffen Strukturen, die über einzelne Projekte hinaus Bestand haben – und Produkte ermöglichen, die nicht nur innovativ sind, sondern auch regulatorisch tragfähig und nachhaltig erfolgreich.
Überblick:
- Design Control in der Medizintechnik: Warum sie unverzichtbar ist
- Die zentralen Elemente der Design Control: Von der Idee zur Freigabe
- Typische Schwächen in der Design Control – und wie man sie vermeidet
- Design Control strategisch nutzen – als Brücke zwischen Entwicklung, Qualität und Zulassung
- Fazit: Design Control als Rückgrat strukturierter Produktentwicklung