Produktionsprozesse optimieren in der Medizintechnik: Effizienz trifft Sicherheit
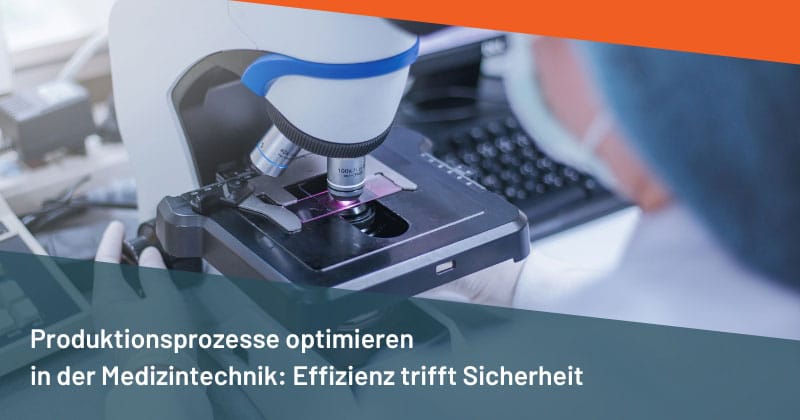
Wer Produktionsprozesse optimieren will, steht in der Medizintechnik vor einer besonderen Herausforderung: Neben Effizienz und Wirtschaftlichkeit müssen höchste Standards in Bezug auf Qualität, Rückverfolgbarkeit und regulatorische Anforderungen erfüllt werden. Optimierung bedeutet hier nicht nur Kostensenkung – sie muss auch Validierbarkeit, Auditfähigkeit und Produktsicherheit gewährleisten.
Im Zentrum stehen Fragen wie: Welche Prozesse lassen sich verschlanken, ohne Compliance-Risiken einzugehen? Wie können Engpässe oder Fehlerquellen frühzeitig identifiziert werden? Und welche Rolle spielen Prozessanalyse, LEAN Management Methoden, Prozessvalidierung und ein belastbares Qualitätsmanagement Medizintechnik für eine nachhaltige Verbesserung?
- Produktionsprozesse optimieren beginnt mit Klarheit über den Ist-Zustand
- Ziele setzen, Prioritäten klären: Was bei der Optimierung zählt
- Produktionsprozesse optimieren im Spannungsfeld von Effizienz und Regulierung
- Von der Maßnahme zum System
- Fazit: Produktionsprozesse optimieren heißt Strukturen stärken
Produktionsprozesse optimieren beginnt mit Klarheit über den Ist-Zustand
Wer Produktionsprozesse optimieren will, muss zuerst verstehen, wie der aktuelle Ablauf tatsächlich funktioniert. Das klingt selbstverständlich, wird in der Praxis aber oft unterschätzt. Prozesse entwickeln sich über Jahre, wachsen mit dem Unternehmen – und weichen nicht selten erheblich von dem ab, was im Prozesshandbuch dokumentiert ist.
In der Medizintechnik kommt ein zusätzlicher Anspruch hinzu: Prozesse dürfen nicht nur wirtschaftlich sein, sie müssen auch stabil, rückverfolgbar und validierbar sein. Änderungen – selbst wenn sie der Effizienz dienen – dürfen keine neuen Risiken für Produktqualität oder regulatorische Anforderungen erzeugen.
Deshalb ist die Prozessanalyse der erste notwendige Schritt. Sie legt offen:
- Welche Schritte tatsächlich durchlaufen werden – nicht nur, was auf dem Papier steht
- Wo Medienbrüche, Wartezeiten oder Schnittstellenprobleme entstehen
- Welche Aktivitäten echten Mehrwert bringen – und welche nicht
- Ob Verantwortlichkeiten, Prüfungen und Freigaben klar geregelt sind
- Welche Varianten bestehen und wie sie die Prozessvalidierung beeinflussen
Nur wenn der Ist-Zustand mit ausreichend Tiefe und Genauigkeit erfasst ist, lässt sich ableiten, wo konkrete Verbesserungen möglich, sinnvoll und zulässig sind.
In vielen Unternehmen führt allein diese erste strukturierte Analyse schon zu ersten Aha-Momenten: Doppelbearbeitungen, unnötige Kontrollschleifen oder veraltete Übergaberoutinen werden sichtbar – und damit auch adressierbar.
Produktionsprozesse optimieren beginnt mit Einsicht. Erst danach folgt die Umsetzung – gezielt, risikobewusst und mit Blick auf langfristige Stabilität.
Ziele setzen, Prioritäten klären: Was bei der Optimierung zählt
Produktionsprozesse optimieren heißt nicht automatisch: schneller oder günstiger produzieren. In der Medizintechnik geht es immer auch um Sicherheit, Stabilität und regulatorische Konformität. Deshalb ist es entscheidend, vor jeder Maßnahme genau zu definieren, was verbessert werden soll – und wo der größte Hebel liegt.
Typische Optimierungsziele können sein:
- Reduktion von Durchlaufzeiten
- Fehlervermeidung und Nacharbeitsminimierung
- Erhöhung der Prozessstabilität
- Bessere Auslastung von Maschinen und Personal
- Senkung der Ausschussquote
- Audit- und Validierungsfähigkeit verbessern
Nicht jedes Ziel ist mit jeder Maßnahme erreichbar – und nicht jede Prozessverbesserung ist im regulierten Umfeld ohne Weiteres umsetzbar. Deshalb braucht es eine klare Priorisierung:
- Welche Verbesserungen zahlen auf Produktsicherheit und regulatorische Anforderungen ein?
- Welche Änderungen benötigen eine neue Prozessvalidierung?
- Welche Maßnahmen können mit vertretbarem Aufwand umgesetzt werden?
- Welche bringen den größten Nutzen bezogen auf operative Exzellenz?
In dieser Phase ist auch die Zusammenarbeit mit den Fachbereichen essenziell: Produktion, Qualität, Regulatory Affairs und Technik müssen gemeinsam bewerten, was möglich und sinnvoll ist – und was nicht. Gerade in stark regulierten Abläufen ist interdisziplinäre Abstimmung der Schlüssel, um Umsetzungszeit zu verkürzen und Risiken zu minimieren.
Ein oft unterschätzter Erfolgsfaktor in der Zieldefinition: Klare Kennzahlen. Ohne messbare Kriterien lässt sich weder der Ist-Zustand sinnvoll bewerten noch der Erfolg einer Maßnahme beurteilen. Hier helfen Methoden aus dem LEAN Management und der Prozessanalyse, die Optimierungsziele greifbar und überprüfbar zu machen.
Produktionsprozesse optimieren im Spannungsfeld von Effizienz und Regulierung
In kaum einer Branche ist der Spielraum für Prozessveränderungen so eng gesteckt wie in der Medizintechnik. Wer Produktionsprozesse optimieren will, muss Effizienzsteigerung und regulatorische Sicherheit gleichzeitig im Blick behalten – und genau darin liegt die Herausforderung.
Während in anderen Industrien Optimierungen oft schnell und iterativ umgesetzt werden können, unterliegt jede Veränderung in der Medizintechnik einer strengen Bewertung:
- Was bedeutet die Änderung für bestehende Nachweise?
- Müssen Validierungen aktualisiert werden?
- Wie wird sichergestellt, dass keine neuen Risiken eingeführt werden?
Die Praxis zeigt: Prozessoptimierung wird hier schnell zum Balanceakt. Auf der einen Seite stehen Zielgrößen wie Durchsatz, Materialeinsatz oder Zykluszeit. Auf der anderen Seite technische Dokumentation, Qualitätsnachweise und Auditsicherheit.
Deshalb ist es essenziell, nicht nur die Prozesse selbst zu analysieren, sondern auch die begleitenden Anforderungen zu verstehen:
- Welche Normen greifen im konkreten Prozessabschnitt?
- Welche regulatorischen Schnittstellen sind betroffen?
- Welche Reportingpflichten müssen erfüllt bleiben?
Wer diese Wechselwirkungen berücksichtigt, vermeidet kostspielige Rückschritte – etwa durch Nachvalidierungen oder Nachfragen in externen Audits. Gleichzeitig wird der Optimierungsprozess selbst belastbarer, weil potenzielle Hürden frühzeitig sichtbar gemacht werden.
Produktionsprozesse optimieren heißt in diesem Kontext: Veränderungen mit Struktur und Weitblick anzugehen – mit einem realistischen Blick auf das, was regulatorisch notwendig und prozessual machbar ist.
Von der Maßnahme zum System
Viele Unternehmen starten mit einzelnen Verbesserungsmaßnahmen – weniger Ausschuss, kürzere Rüstzeiten, bessere Linienauslastung. Doch wer Produktionsprozesse optimieren will, braucht mehr als punktuelle Eingriffe. Nachhaltige Prozessverbesserung entsteht nur dann, wenn daraus ein übergreifendes, tragfähiges System wird.
Das bedeutet: Optimierung wird nicht als Projekt behandelt, sondern als Prinzip.
Typische Merkmale eines systemischen Ansatzes:
- Strukturierter Verbesserungsprozess: Änderungen folgen klaren Abläufen – von der Identifikation über Bewertung und Umsetzung bis zur Wirksamkeitskontrolle.
- Dokumentation und Rückverfolgbarkeit: Alle Optimierungsmaßnahmen sind nachvollziehbar dokumentiert – auch im Hinblick auf interne oder externe Audits.
- Einbindung aller Beteiligten: Optimierung ist nicht Aufgabe einer Abteilung, sondern ein organisationsweites Thema. Produktion, Qualität, Technik und Regulatory müssen abgestimmt agieren.
- Regelmäßige Prozessreviews: Optimierungen werden nicht abgeschlossen, sondern fortlaufend bewertet und bei Bedarf angepasst.
- Klar definierte Metriken: Erfolg wird messbar gemacht – mit konkreten Zielwerten für Qualität, Durchsatz, Ausschuss oder Kosten.
Nur wenn Optimierung konsequent als Teil der betrieblichen Steuerung etabliert wird, wirkt sie dauerhaft. Es entsteht ein Rahmen, in dem jede Verbesserung greift – weil sie in bestehende Abläufe, Verantwortlichkeiten und Systeme eingebettet ist.
Produktionsprozesse optimieren wird damit zu einem Baustein der Unternehmensstrategie: nicht impulsgetrieben, sondern systematisch, überprüfbar und auf nachhaltige Wirkung ausgelegt.
Fazit: Produktionsprozesse optimieren heißt Strukturen stärken
Wer Produktionsprozesse optimieren will, braucht mehr als Tools oder Projektpläne – es geht um ein tiefes Verständnis der realen Abläufe, klare Zieldefinitionen und den Mut, Strukturen neu zu denken. In der Medizintechnik kommt die zusätzliche Verantwortung hinzu, Qualität und regulatorische Anforderungen jederzeit sicherzustellen.
Effizienz entsteht dort, wo Prozesse transparent, validierbar und messbar sind. Deshalb beginnt Optimierung mit Analyse und Priorisierung – und wirkt dann, wenn sie nicht vereinzelt bleibt, sondern als systematischer Teil der Unternehmensführung verankert ist.
Unternehmen, die ihre Produktionsprozesse konsequent weiterentwickeln, schaffen nicht nur wirtschaftliche Vorteile, sondern auch eine belastbare Grundlage für Wachstum, Innovation und regulatorische Sicherheit.
Überblick:
- Produktionsprozesse optimieren beginnt mit Klarheit über den Ist-Zustand
- Ziele setzen, Prioritäten klären: Was bei der Optimierung zählt
- Produktionsprozesse optimieren im Spannungsfeld von Effizienz und Regulierung
- Von der Maßnahme zum System
- Fazit: Produktionsprozesse optimieren heißt Strukturen stärken