Prozessvalidierung in der Medizintechnik: Sicherheit nachweisbar machen
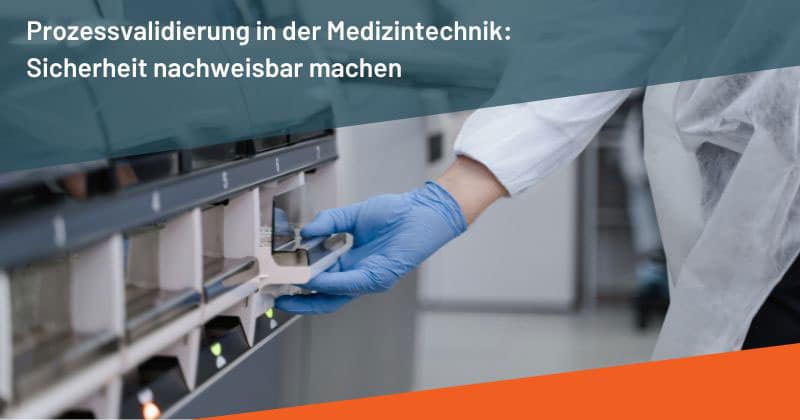
Die Prozessvalidierung gehört zu den zentralen Anforderungen in der Medizintechnik. Sie stellt sicher, dass Produktions- und Prüfprozesse unter festgelegten Bedingungen zuverlässig und reproduzierbar Ergebnisse liefern – und damit zur Produktsicherheit, Wirksamkeit und regulatorischen Konformität beitragen.
Anders als bei Routinekontrollen reicht es nicht aus, dass ein Prozess funktioniert – seine Leistungsfähigkeit muss dokumentiert, nachvollziehbar belegt und dauerhaft sichergestellt werden. Gerade deshalb zählt die Prozessvalidierung zu den anspruchsvollsten Disziplinen im Qualitätsmanagement Medizintechnik.
Im Fokus stehen dabei nicht nur klassische Fertigungsprozesse, sondern auch Abläufe in Entwicklung, Reinigung, Verpackung oder Softwareprüfung. Für Unternehmen bedeutet das: Wer seine Prozesse validieren will, braucht ein strukturiertes Vorgehen, technisches Verständnis, klare Verantwortlichkeiten – und die Fähigkeit, regulatorische Anforderungen mit operativer Exzellenz, CAPA Management, Root Cause Analysis und Design Control zu verbinden.
Überblick:
- Warum Prozessvalidierung in der Medizintechnik unverzichtbar ist
- Strukturiert validieren: Phasen, Verantwortlichkeiten, Dokumentation
- Typische Fehler in der Prozessvalidierung – und wie man sie vermeidet
- Prozessvalidierung strategisch nutzen: Von der Pflicht zur Stärke
- Fazit: Prozessvalidierung als Fundament für Qualität und Vertrauen
Warum Prozessvalidierung in der Medizintechnik unverzichtbar ist
In der Medizintechnik ist es nicht ausreichend, dass ein Prozess „funktioniert“. Es muss nachgewiesen werden, dass er wiederholt und verlässlich das gewünschte Ergebnis liefert – unabhängig davon, wer ihn ausführt oder unter welchen Randbedingungen er stattfindet. Genau hier setzt die Prozessvalidierung an.
Sie schafft regulatorische Sicherheit, indem sie die Leistungsfähigkeit eines Prozesses systematisch überprüft und dokumentiert. Nur validierte Prozesse dürfen für produktkritische Tätigkeiten eingesetzt werden – das gilt insbesondere in Bereichen wie:
- Herstellung steriler Produkte
- Reinigung und Verpackung
- Prüfverfahren mit hohem Einfluss auf die Freigabe
- Softwaregesteuerte Prozesse, deren Ergebnisse nicht vollständig verifiziert werden können
Dabei geht es nicht nur um eine formale Anforderung der Normen – Prozessvalidierung schützt direkt die Produktsicherheit. Fehler in der Validierung können zu unentdeckten Schwachstellen führen, die sich erst spät oder gar nicht in der Prüfung zeigen – mit potenziell gravierenden Folgen für Patientensicherheit, Zulassungsfähigkeit und Marktverfügbarkeit.
Für Unternehmen heißt das: Prozesse, die nicht validiert sind oder deren Validierung nicht mehr den aktuellen Standards entspricht, stellen ein hohes Risiko dar. Sie gefährden nicht nur die Compliance, sondern auch Lieferfähigkeit, Markenvertrauen und unter Umständen das Haftungsrisiko.
Prozessvalidierung ist daher kein einmaliger Akt, sondern ein wiederkehrender Nachweis: über Planung, Durchführung, Dokumentation – und die Fähigkeit, auf Abweichungen gezielt zu reagieren.
Strukturiert validieren: Phasen, Verantwortlichkeiten, Dokumentation
Eine wirksame Prozessvalidierung folgt keinem starren Schema, sondern einem nachvollziehbaren, dokumentierten Ablauf, der sowohl regulatorische Anforderungen erfüllt als auch zur tatsächlichen Prozesssicherheit beiträgt. Entscheidend ist, dass jede Validierung nachweisbar reproduzierbare Ergebnisse liefert – nicht nur im Labor, sondern im laufenden Betrieb.
Der Validierungsprozess gliedert sich in drei zentrale Phasen:
1. IQ – Installationsqualifizierung
Ziel: Nachweis, dass die verwendeten Maschinen, Anlagen oder IT-Systeme korrekt installiert wurden – gemäß Herstellerspezifikationen, internen Anforderungen und geltenden Normen.
Hierzu zählen u. a. Kalibrierungen, Dokumentenprüfungen, Anlagenqualifikationen und die Freigabe der Umgebung.
2. OQ – Funktionsqualifizierung
Ziel: Nachweis, dass der Prozess innerhalb definierter Betriebsgrenzen stabil funktioniert. Hier werden kritische Parameter identifiziert und unter realitätsnahen Bedingungen getestet – z. B. Temperaturen, Drücke, Zykluszeiten, Materialchargen.
3. PQ – Leistungsqualifizierung
Ziel: Nachweis, dass der Prozess im regulären Betrieb unter Routinebedingungen wiederholt das gewünschte Ergebnis liefert. Typisch sind drei aufeinanderfolgende Serien mit produktionsnahen Bedingungen und vollständiger Dokumentation.
Diese drei Phasen bilden das Rückgrat der Prozessvalidierung. Doch erst mit klar geregelten Verantwortlichkeiten – etwa für Planung, Durchführung, Review und Genehmigung – wird aus dem Verfahren ein belastbarer Nachweis. Eine saubere Dokumentation aller relevanten Schritte, Ergebnisse, Abweichungen und Maßnahmen ist dabei essenziell – nicht zuletzt mit Blick auf Audits oder Inspektionen.
Hinzu kommt: Die Validierung endet nicht mit dem PQ-Bericht. Prozessänderungen, neue Materialien, Software-Updates oder veränderte Rahmenbedingungen können jederzeit eine Revalidierung erforderlich machen. Auch hier gilt: Keine Maßnahme ohne strukturierten Nachweis.
Eine gut geführte Prozessvalidierung gibt Sicherheit – technisch, rechtlich und organisatorisch.
Typische Fehler in der Prozessvalidierung – und wie man sie vermeidet
Prozessvalidierung ist kein formaler Haken auf einer Checkliste – sie ist ein belastbarer Nachweis für die Fähigkeit eines Prozesses, unter Routinebedingungen zuverlässig zu funktionieren. Doch in der Praxis zeigt sich immer wieder: Viele Validierungen sind formal korrekt, aber inhaltlich schwach – oder sie verlieren durch unzureichende Pflege ihre Aussagekraft.
Hier sind die häufigsten Fehlerquellen – und wie man sie konsequent ausschließt:
1. Unklare Prozessdefinition
Wenn Eingangsgrößen, Prozessparameter oder erwartete Ergebnisse nicht exakt beschrieben sind, lässt sich auch keine stabile Leistung nachweisen.
Lösung: Vor jeder Validierung muss eine saubere Prozessanalyse erfolgen – mit klaren Sollgrößen und nachvollziehbaren Grenzen.
2. Fehlende Risikobewertung
Wird nicht definiert, welche Parameter kritisch sind, können Abweichungen nicht sinnvoll bewertet werden.
Lösung: Die Validierung sollte immer mit einer risikobasierten Betrachtung verknüpft werden – etwa im Sinne eines dokumentierten Ansatzes nach GAMP5 oder FMEA.
3. Lückenhafte Dokumentation
Selbst ein technisch korrekt validierter Prozess gilt als nicht validiert, wenn Unterlagen unvollständig oder widersprüchlich sind.
Lösung: Dokumentationsanforderungen müssen von Anfang an klar geregelt sein – inklusive Rohdaten, Prüfprotokolle, Abweichungsberichte und Review-Prozesse.
4. Keine Revalidierungsstrategie
Wird ein Prozess nach Änderungen weiter betrieben, ohne neu validiert zu werden, entsteht ein Compliance-Risiko – oft unbemerkt.
Lösung: Ein strukturierter Validierungs-Lebenszyklus mit klaren Auslösekriterien für Revalidierungen ist Pflicht – verankert im Qualitätsmanagement Medizintechnik.
5. Keine Rückkopplung mit dem CAPA-Prozess
Wird bei Fehlern nicht geprüft, ob die Prozessvalidierung lückenhaft war, bleiben strukturelle Schwächen bestehen.
Lösung: Jede signifikante Abweichung in Produktion oder Audit sollte mit Blick auf die Validierung reflektiert werden – auch als Bestandteil des CAPA Management.
Diese Schwächen lassen sich vermeiden – durch Planung, strukturierte Verantwortung und ein Verständnis dafür, dass Prozessvalidierung keine Dokumentationsübung ist, sondern ein zentrales Sicherheits- und Steuerungsinstrument.
Prozessvalidierung strategisch nutzen: Von der Pflicht zur Stärke
In vielen Unternehmen wird Prozessvalidierung vor allem als regulatorische Pflicht wahrgenommen – aufwendig, zeitkritisch, dokumentationsintensiv. Dabei liegt gerade in der systematischen Validierung ein enormes strategisches Potenzial. Sie zwingt dazu, Prozesse vollständig zu durchdringen, kritische Parameter zu definieren und ihre Stabilität messbar zu machen. Und genau das schafft die Basis für belastbare, auditfeste und effizient steuerbare Produktions- und Prüfabläufe.
Wer Validierung als integralen Bestandteil der Prozessentwicklung versteht, legt damit den Grundstein für reproduzierbare Qualität. Es entsteht ein klarer Rahmen: für Verantwortlichkeiten, Grenzwerte, Prüfmechanismen und Reaktionsstrategien. Damit wird Validierung nicht zur lästigen Pflicht, sondern zur Absicherung von Effizienz, Produktsicherheit und Zulassungsfähigkeit – gerade in stark regulierten Märkten.
Ein strategischer Umgang mit Prozessvalidierung zeigt sich auch im Zusammenspiel mit anderen Qualitätsinstrumenten. Erkenntnisse aus der Root Cause Analysis können direkt in Revalidierungen einfließen. Validierungsergebnisse wiederum liefern wertvolle Daten für das Risikomanagement, die Prozessoptimierung und das Design Control in frühen Entwicklungsphasen. Richtig genutzt, wird die Validierung zur Brücke zwischen operativem Tagesgeschäft und übergeordnetem Qualitätsanspruch.
Ein weiterer Vorteil: Unternehmen, die Validierungen nicht nur durchführen, sondern methodisch weiterentwickeln, gewinnen Geschwindigkeit – im Änderungsmanagement, bei Zulassungen oder bei der Einführung neuer Technologien. Validierte Prozesse schaffen Vertrauen: intern, bei Auditoren und bei Behörden. Und genau dieses Vertrauen ist es, das langfristige Wettbewerbsfähigkeit im Markt sichert.
Fazit: Prozessvalidierung als Fundament für Qualität und Vertrauen
Prozessvalidierung ist mehr als eine regulatorische Anforderung – sie ist ein zentraler Baustein für reproduzierbare Qualität, Produktsicherheit und unternehmerische Stabilität. Wer Validierung früh im Prozess berücksichtigt und strategisch einsetzt, schafft nicht nur Compliance, sondern ein starkes Fundament für langfristige Effizienz und Innovationsfähigkeit.
Der Schlüssel liegt dabei nicht nur in der technischen Durchführung, sondern im strukturellen Denken: Prozesse müssen analysiert, Verantwortlichkeiten klar geregelt, und Validierungsergebnisse gezielt ausgewertet und genutzt werden. Unternehmen, die Prozessvalidierung konsequent mit Instrumenten wie Root Cause Analysis, Design Control oder einem strukturierten Programmmanagement verbinden, entwickeln ein System, das Fehler nicht nur erkennt – sondern verhindert, bevor sie entstehen.
So wird aus der Pflicht zur Dokumentation ein Wettbewerbsvorteil: robust, nachvollziehbar und zukunftsfähig.
- Warum Prozessvalidierung in der Medizintechnik unverzichtbar ist
- Strukturiert validieren: Phasen, Verantwortlichkeiten, Dokumentation
- Typische Fehler in der Prozessvalidierung – und wie man sie vermeidet
- Prozessvalidierung strategisch nutzen: Von der Pflicht zur Stärke
- Fazit: Prozessvalidierung als Fundament für Qualität und Vertrauen