Wie läuft eine CAPA ab?
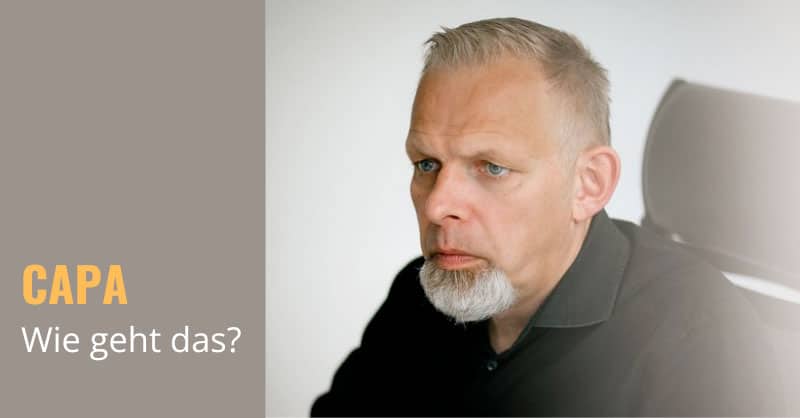
CAPA steht für Corrective Action and Preventive Action. Sie ist notwendig, weil in der Medizintechnik und industriellen Produktion es immer wieder zu Ausfällen, Compliance-Fehler oder fehlerhaften Werkstücken kommt.
Wenn das passiert, wird eine CAPA gestartet. Ein großes Problem ist allerdings, dass viele Firmen sofort CAPAs starten, auch wenn das manchmal überhaupt nicht notwendig ist.
Dieser Beitrag beschränkt sich auf die Methodik. Tipps und Hilfestellungen, wie man mit einer CAPA und dem gesamten CAPA-Managementsystem, also der Vielzahl an CAPAs, die man zu bearbeiten hat, am besten umgeht, geben wir in weiteren Beiträgen.
CAPA ist in der Norm 13485 genau erläutert. Allerdings sind Standards häufig etwas missverständlich beschrieben und können daher unterschiedlich interpretiert werden.
Sie sehen gerade einen Platzhalterinhalt von YouTube. Um auf den eigentlichen Inhalt zuzugreifen, klicken Sie auf die Schaltfläche unten. Bitte beachten Sie, dass dabei Daten an Drittanbieter weitergegeben werden. Mehr Informationen
Woraus besteht eine CAPA?
1. Problembeschreibung
2. Sofortmaßnahme/Containment Action
3. Korrektur
4. Ursachenanalyse
5. Korrektive Maßnahme
6. Verifikation
7. Kontrolle
8.1 Zurück zum Anfang
8.2 Optional: Erfolgsfeier
1. Problembeschreibung
Die Problembeschreibung muss so präzise und gut sein, dass Sie eventuell schon aus der Problembeschreibung auf eine Ursache und damit auf eine korrektive Aktion abzielen können.
Dafür beschreiben Sie sowohl den IST- als auch den Ziel-Zustand, am besten mit Fakten und Zahlen. Die Differenz zwischen diesen beiden Zuständen ist das, was verbessert werden muss.
Beispiel:
Ihre Teile sollen alle mit einer Toleranz von 10,5mm +/-1 ausgeliefert werden. Das ist das Ziel. Ein defektes Teil ist ein Teil, das außerhalb der Toleranz liegt, z.B. bei dem 10,3mm gemessen wurden.
Der IST-Zustand lautet dann: Ich habe ein fehlerhaftes Teil, das 10,3 Millimeter als Messergebnis hat. Und der Ziel-Zustand: Jedes Teil soll 10,5 Millimeter +/-1 betragen.
Daraus lässt sich bereits erahnen, dass irgendwas in dem Fertigungsprozess nicht richtig gelaufen ist.
2. Sofortmaßnahme/Containment Action
Als nächstes muss verhindert werden, dass weiterhin fehlerhafte Teile an den Kunden geliefert werden. Dafür stelle ich das Problem ab.
Es ist wichtig, das so schnell wie möglich zu machen. Denn Sie wollen ja verhindern, dass weiterhin fehlerhafte Teile bei Ihrem Kunden ankommen.
Zudem müssen Sie sich ebenfalls fragen: Könnten eventuell andere Teile betroffen sein?
Sie dokumentiere Ihre kurze Untersuchung dazu und ebenfalls, was Sie getan habe, damit der Fehler nicht mehr den Kunden erreicht.
Beispiel:
Sie führen eine extra Kontrolle auf meine Maßhaltigkeit ein. Bevor das Teil, das 10,5mm +/-1mm als Toleranz haben soll, das Werk verlässt, überprüfen Sie, ob das zutrifft und sortieren alle falsche Teile aus. Das wäre eine klassische Containment Action.
Beispiel 2:
Im Falle eines Wasserrohrbruchs drehen Sie allererstes den Haupthahn zu, bevor Sie weitere Untersuchungen anstelle. Denn Sie möchten ja, dass das Wasser aufhört zu laufen.
„Stop the bleeding“, sagen unsere amerikanischen und englischen Freunde häufig dazu. Also Pflästerchen draufmachen, damit erst mal die Blutung gestillt ist. Erst dann machen Sie sich daran zu klären, was wirklich die Ursache hinter dem Problem ist.
3. Korrektur
Die Korrektur(-maßnahme) oder die Korrektur ist keine korrektive Maßnahme oder gar präventive Maßnahme, wie es häufig in der Literatur oder auch auf Vorträgen fälschlicherweise gesagt wird.
Eine Korrektur bezieht sich nur auf das eine defekte Teil.
Beispiel:
Angenommen Sie haben vom Kunden ein defektes Teil zurückbekommen, dann können Sie es durch Nacharbeit in einen „Gut“-Zustand überführen. Oder Sie bieten dem Kunden direkt ein „Gut“-Teil an, ohne dass er das defekte Teil zu Ihnen schicken muss. Natürlich müssen Sie vorher überprüfen, dass neue Teil auch wirklich fehlerfrei ist.
4. Ursachenanalyse
Jetzt geht es darum, zu analysieren, warum der Fehler aufgetreten ist: Warum ist das ursächlich passiert?
5-Why-Methode:
Sie fragen sich sukzessive durch Warums durch. Warum ist das passiert? Warum ist wiederum das passiert? Usw. Wenn Sie fünf Mal das Warum stellen, habe Sie meistens eine Ursache gefunden.
Fishbone-Diagramm/6M-Methode, falls das Problem komplexer ist:
Sie versuchen alle potentiellen Fehlerquellen abzudecken: Mensch, Maschine, Methode, Umwelt, Management oder auch die Messung an sich.
Die einzelnen Punkte schreiben Sie an die einzelnen Fischgräten ran. Das macht man am besten in einem Team gemeinsam mit Experten, Ingenieuren usw., die sich technisch auskennen. Manchmal braucht man auch Einkäufer usw. Deshalb bilden Sie ein Team und machen eine Session von 60 bis 90 Minuten. Und dann hat man meistens schon Hinweise darauf, was die Ursache war.
Wenn Sie aber mehrere Ursachen hinter dem Defekt vermuten, müssen Sie natürlich jeden dieser Äste bzw. Fischgräten ablaufen und bis zum Ende zu gehen und sich zu überlegen – vielleicht auch durch Tests feststellen –, ob das die Ursache hinter dem Fehler ist, oder ob es nur einen Einfluss hat
und die Ursache immer noch nicht gefunden wurde.
Für die Ursachenanalyse sollten Sie sehr viel Zeit darauf verwenden. Sie muss präzise und vollumfänglich sein.
5. Korrektive Maßnahme
Die korrektive Maßnahme ist die Maßnahme, um die Ursache für den Fehler auszumerzen. Und das geht am besten, wenn man sich wie einen Lichtschalter vorstellt:
Stellen Sie den Lichtschalter an, werden ich defekte Teile produziert. Stellen Sie den Lichtschalter aus, haben Sie nur noch „Gut“-Teile, die Ihre Produktion verlassen.
6. Verifikation
Hinter jeder von der möglichen Korrekturmaßnahmen muss eine Verifikation gefahren werden. Sie müssen belegen, dass die korrektive Maßnahme, die Sie durchgeführt haben, wirklich funktioniert und das Problem ursächlich abstellt.
„Schalter an/aus“ ist die beste Methode, um zu prüfen, ob die Ursache gefunden wurde.
Exkurs:
Das gilt auch für präventive Maßnahmen. Allerdings habe ich sehr selten welche gesehen. Häufig werden korrektive Maßnahmen als präventive Maßnahmen ausgegeben, weil man meint, wenn ich die korrektive Maßnahme, die ich gebracht habe, in einen anderen Bereich überführe, wäre das präventiv. Das stimmt aber nicht unbedingt. Sie versuchen dann nur, das gleiche Problem woanders zu vermeiden.
Erst wenn ich die korrektive Maßnahme in eine neue Produktentwicklung oder ähnliches einführe, kann man von einer präventiven Maßnahme sprechen.
7. Kontrolle
Sie legen fest, wie viele Teile Sie messen möchten und verfolgen anschließend, dass Sie mit der verifizierten, korrektiven Maßnahme nur noch „Gut“-Teile produzieren. Bevor die Teile an die Kunden verschickt werden, muss prüft werden, ob der vorher definierte Toleranzbereich nicht überschritten wurde.
Denn eines dürfen Sie auf keinen Fall tun: Dem Kunden erneut defekte Teile zusenden. Denn um das zu verhindern, haben Sie ja bereits die Sofortmaßnahme/Containment Action eingeführt.
Das gleiche gilt auch für Prozesse, Compliance Themen etc.
8.1 Zurück zum Anfang
Falls bei der Kontrolle defekte Teile auftauchen, müssen Sie wieder zurück zum Start. Es kann sein, dass Sie nochmal bei der Problembeschreibung anfangen oder aber die Ursachenanalyse erneut durchführen müssen. Oder es müssen andere korrektive Maßnahmen eingeführt werden.
Dass man vorher nicht weiß, ob man am Ende die Ursache ausmerzen konnte, um das gewünschte Zielergebnis zu erreichen, ist die Arbeit an CAPAs so unheimlich frustrierend.
8.2 Erfolgsfeier
Daher ist es umso wichtiger, dass bei erfolgreicher Durchführung der Kontrolle keine defekten Teile mehr aufkommen, das Team den Erfolg auch feiert.
Gratulation! Ihr Team hat eine weitere Herausforderung gemeistert, eine weitere Qualitätsmaßnahme eingeführt und Ihr Produkt verbessert.